
Leinco Technologies specializes in cell banking services, including master cell bank (MCB) and working cell bank (WCB) preparation, ensuring a reliable supply of high-quality cells for your research and manufacturing needs.
As an ISO 9001:2015 certified and GMP-compliant custom manufacturer, we excel in producing monoclonal antibodies and recombinant proteins for diagnostics and preclinical research. Our state-of-the-art facility accommodates both large and small-scale production, guaranteeing consistent quality and adherence to industry standards.
Partner with Leinco for dependable cell banking solutions and expert antibody manufacturing services.
What’s the difference between MCB and WCB?
The master cell bank is created from a single cell source optimized for monoclonal antibody production. Cells are expanded to a level required to freeze an appropriate number of vials based on demand for their use. Master cell banking includes testing cell banks for recovery viability after cryopreservation. Biosafety testing and cell line authentication are also part of master cell banking. The scope of biosafety testing and authentication is determined based on the client-specific application and advice from the worldwide regulatory bodies.
The working cell bank (WCB) is created from the expansion of a master cell bank vial. Expansion and cryopreservation of the working cell bank depends on the demand for use. It is the working cell bank that is used by cell culture manufacturing scientists to produce the seed culture for inoculation of bioreactors. Leinco Technologies offers custom In vitro Antibody and Protein Production in stirred tank and hollow fiber bioreactors.
The first step in a quality manufacturing system is to assure creation of master cell banks (MCB) and working cell banks (WCB). Leinco Technologies uses a tiered cell banking system to ensure a consistent supply of characterized cells for use in continuous cycle manufacturing campaigns. Cell banking work is performed in dedicated cleanroom suites using standard operating procedures and data from the preparation of cell banks is recorded in detailed batch records.
Mycoplasma (-) Negative Testing
As part of the master cell banking and working cell banking process, all cell lines are tested and certified to be mycoplasma negative (-). Mycoplasma are a group of bacteria that lack a cell wall around their cell membrane making them resistant to most antibiotics. The presence of mycoplasma in a cell culture could induce cellular changes including chromosomal aberrations, changes in metabolism and cell growth.
This certification is necessary to not only prevent the contamination of other cell lines during the cell culture process, but to avoid the detrimental effects mycoplasma contamination may have on protein or antibody expression. It is estimated that 15% of US labs and up to 60% of Asian Labs are contaminated with mycoplasma. The top 5 reasons and benefits to test and certify your cell lines are as follows:
- Worldwide estimates are 35% of existing cell banks may be contaminated
- Loss of engineered cell lines that took many months or years to create
- Major impact on data reliability and reproducibility
- Testing is required by many journals for publication and by regulatory agencies
- Loss of financial resources such as grants dependent on specific cell lines
It is the policy of Leinco Technologies to thaw all cells in a quarantined clean room suite. All incoming vials are tested for mycoplasma contamination while in quarantine. If the initial mycoplasma test is negative, the cell line will be expanded for potential cryopreservation of sufficient back up vials.
Clonality, Productivity, and Optimization Testing
To ensure optimal in vitro monoclonal antibody production, it’s crucial to assess your cell line’s performance. Clonality and specific productivity rate (SPR) assays are essential tools to determine the percentage of antibody-producing cells and their titer consistency.
Maximizing monoclonal antibody yield starts with cell line optimization during master cell bank (MCB) creation. Skipping this critical step risks selecting non-producing cells, hindering productivity in bioreactors or during adaptation to protein-free, animal component-free media.
Invest in cell line optimization to enhance your monoclonal antibody production efficiency and ensure a reliable, high-quality supply.
Some of the benefits include:
- Optimization of cells for cGMP manufacturing
- Quality Control Checks – viability, clonality, sequencing, sterility, pre/post IEF, pathogen (-), mycoplasma (-)
- Certification free of adventitious agents including:
- Master Cell Bank
- Pathogen (-) reporting
- Mycoplasma (-) reporting provided
- Freeze 30+ vials or more
Protein-Free, Animal Origin-Free Cell Culture: Enhancing Biopharmaceutical Production
Mammalian cell lines like CHO, NSO, HEK-293, and hybridomas can thrive in chemically defined, protein-free, animal origin-free media. This adaptation streamlines bioreactor production of recombinant proteins and antibodies, simplifying downstream processing and ensuring a final product free of animal components.
Adopting protein-free cell culture enhances biopharmaceutical manufacturing by:
- Improving product purity: Eliminating animal-derived components reduces contamination risks and simplifies purification processes.
- Increasing consistency: Chemically defined media ensures consistent cell growth and product quality.
- Facilitating regulatory compliance: Animal origin-free systems align with stringent regulatory requirements for biopharmaceuticals.
Explore the benefits of protein-free, animal origin-free cell culture for your biopharmaceutical production needs.
Cryopreservation
A critical part of manufacturing monoclonal antibodies and proteins is the generation and cryopreservation of the MCB. This assures consistent quality production well into the future. MCB is prepared by performing multiple rounds of single cell cloning and testing until the cells are optimized for production and safe for cryopreservation. Upon agreement of the appropriate scope of work, cell banks are prepared according to guidance established by international regulatory agencies such as the FDA, USDA or EMEA. Each cell bank prepared is tested for mycoplasma and sterility. Testing for adventitious agents is dependent on the final application for each cell bank. The exact number of vials to be cryopreserved is dependent on regulatory guidelines and future production requirements.
Benefits of Master Cell Banking
- Automated cryogenic refrigeration equipment
- All units contain local and remote alarm systems
- Cell lines are maintained at -150ºC or lower
- Restricted access to freezers
- Electronic inventory system
- Dual site backup available
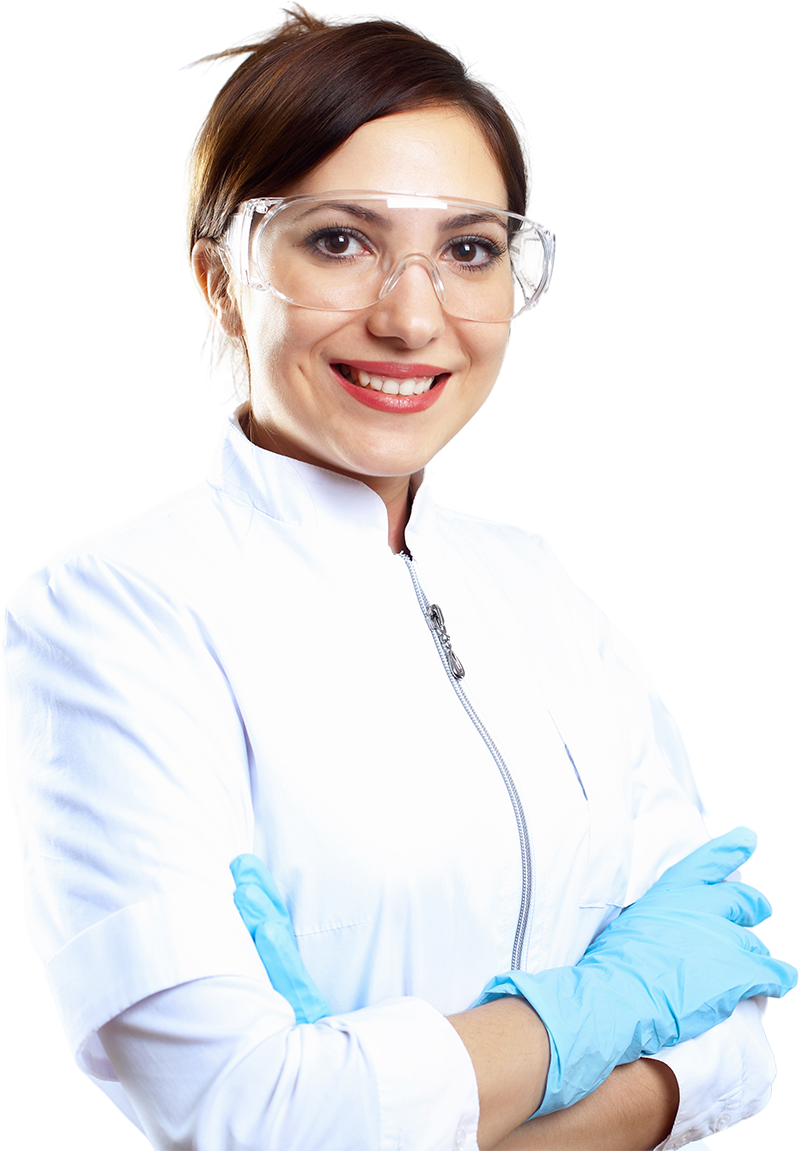